- Model NO.:
- DTS-X
- Certification:
- CE, ISO9001, ISO14001, Dosh,ASME, SGS, TUV, BV, Eac,Crn,Mom,PED
ntent="" style="background-color:#c5e1b3;padding:0 10px;margin:0;line-height:36px;text-align:left;">Product Description
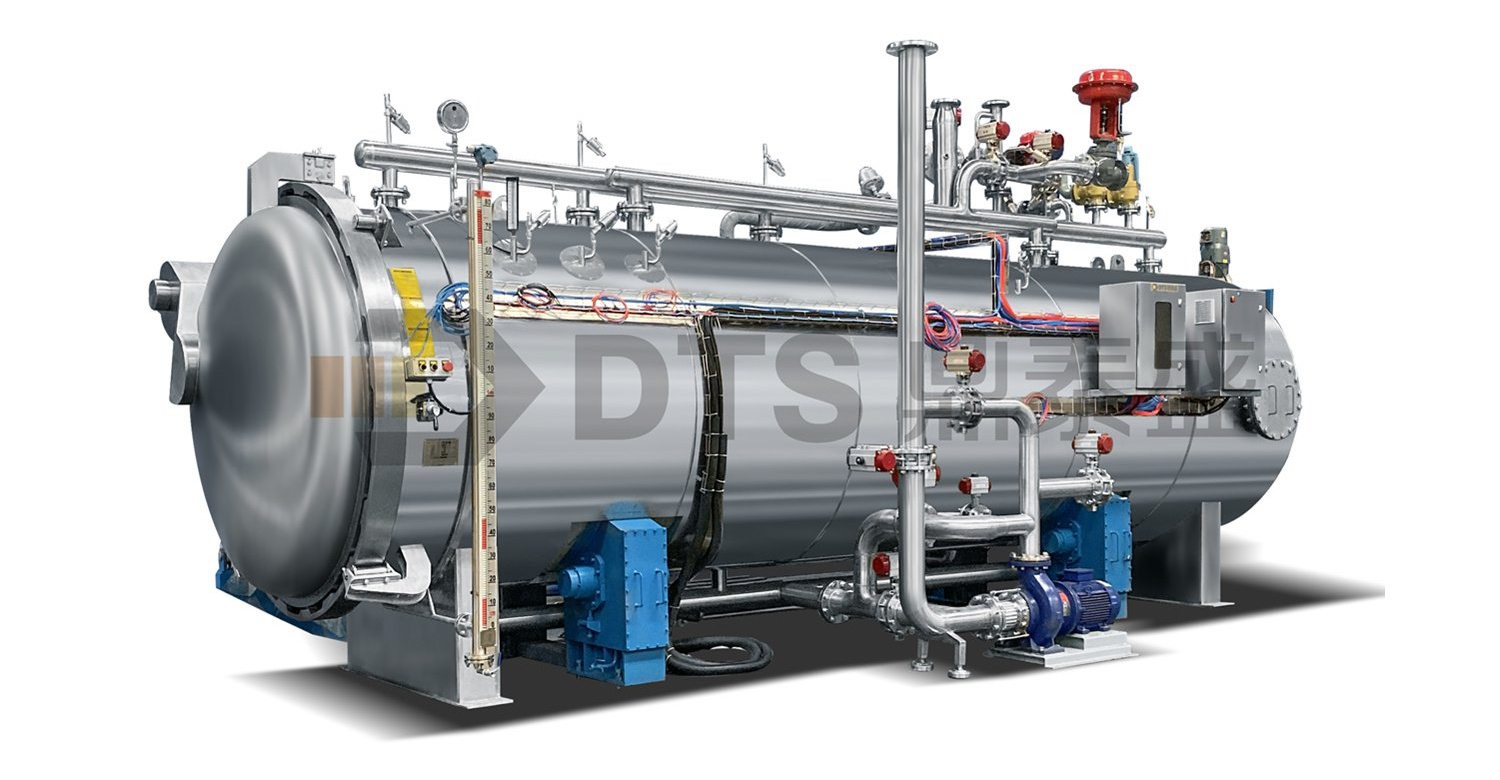
The water spray rotary sterilization retort uses the rotation of the rotating body to make the contents flow in the package. Heat up and cool down by the heat exchanger, so the steam and cooling water will not contaminate the product, and no water treatment chemicals are needed. The process water is sprayed onto the product through the water pump and the nozzles distributed in the retort to achieve the purpose of sterilization. Accurate temperature and pressure control can be suitable for a variety of packaged products.
ntent="" style="background-color:#c5e1b3;padding:0 10px;margin:0;line-height:36px;text-align:left;">Working Principle
Put the product into the sterilization retort, cylinders are individually compressed and close the door. The retort door is secured by triple safety interlocking. Throughout the whole process, the door is mechanically locked.
The sterilization process is automatically carried out according to the recipe input to the micro-processing controller PLC.
Keep an appropriate amount of water at the bottom of the retort. If necessary, this part of water can be injected automatically at the beginning of the heating up. For hot-filled products, this part of water can be preheated first in the hot water tank and then injected. During the entire sterilization process, this part of water is repeatedly circulated by the pump through the water distribution pipe and nozzles distributed in the retort, and the water is sprayed in the form of a mist and evenly distributed in the retort to heat the product. This ensures an even distribution of heat.
Equip the spiral-tube heat exchanger for the sterilization retort and at the heating and cooling stages, the process water passes through one side, and the steam and cooling water pass through the other side, so that the sterilized product will not directly contact the steam and cooling water to realize aseptic heating and cooling.
Throughout the whole process, the pressure inside the retort is controlled by the program by feeding or discharging compressed air through the automatic valve to the retort. Due to water spray sterilization, the pressure in the retort is not affected by temperature, and the pressure can be set freely according to the packaging of different products, making the equipment more widely applicable (three-piece cans, two-piece cans, flexible packaging bags, glass bottles, plastic packaging etc.).
When the sterilization process is finished, an alarm signal will be issued. At this time, the door can be opened and unloaded. Then prepare to sterilize the next batch of products.
The uniformity of temperature distribution in the retort is +/-0.5ºC, and the pressure is controlled at 0.05Bar. During the whole process, the rotation speed and time of the rotating body are determined by the sterilization process of the product.
ntent="" style="background-color:#c5e1b3;padding:0 10px;margin:0;line-height:36px;text-align:left;">Detailed Photos
1. Spiral tube heat exchanger
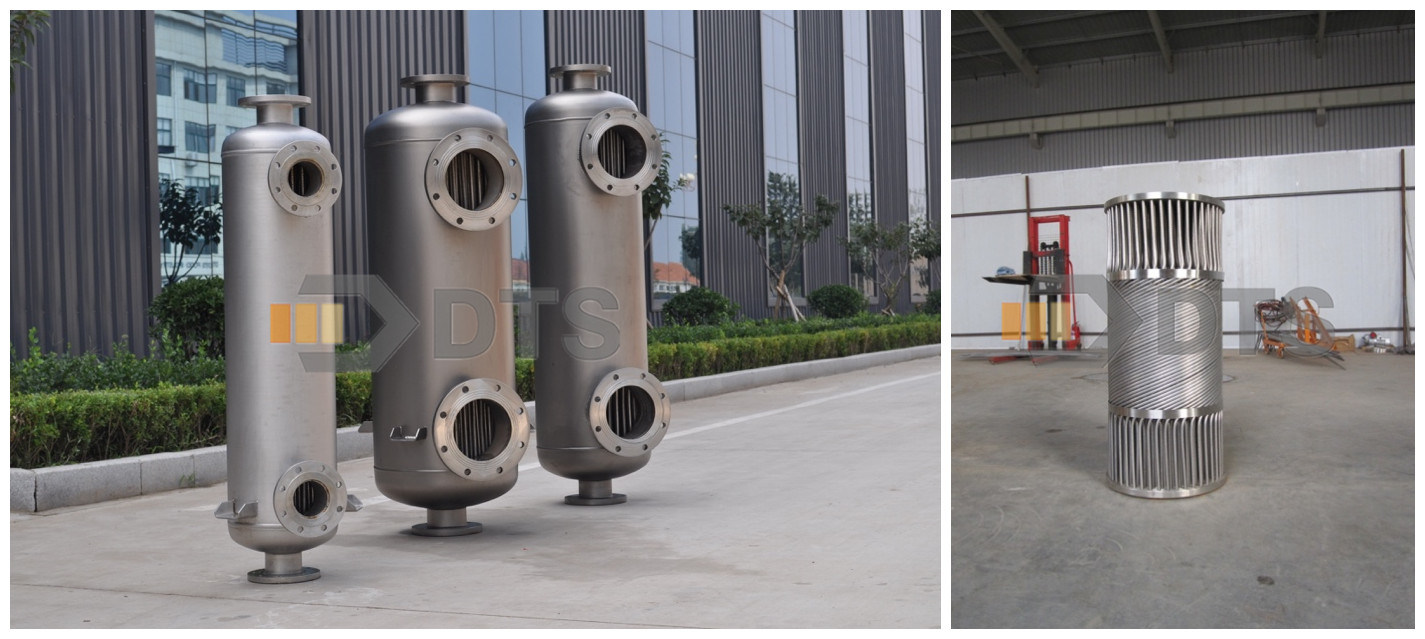
DTS patented tube heat exchanger. Inside tube material is stainless steel 316L, no need to replace the rubber gasket, no need maintenance, corrosion resistance, long service life.
2. Safety interlockManual swing open door with safety interlock.
Option: Space-saving gullotine door with hydraulic driven.
Retorts have intrinsically safe door locking mechanisms with electrical switches interlocked with the internal vessel pressure.
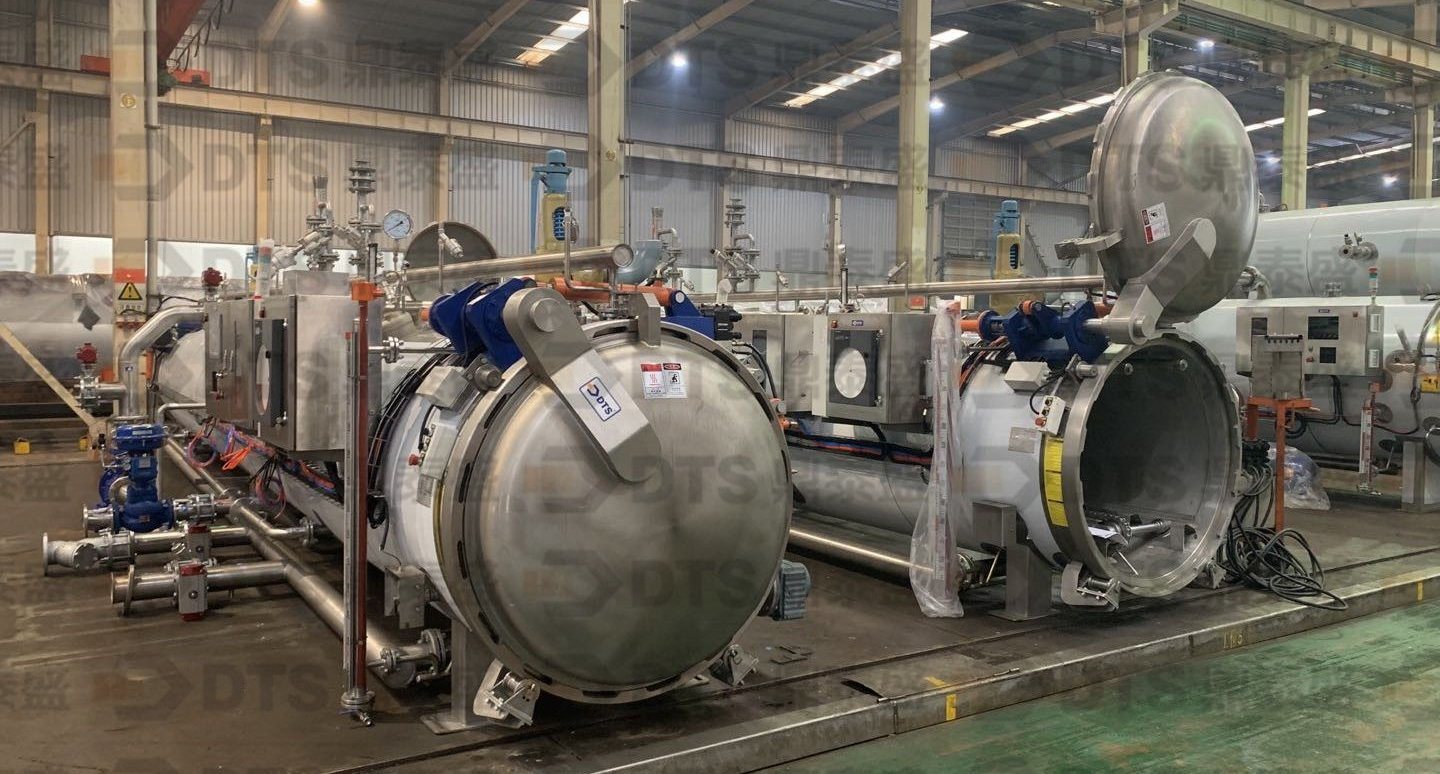
3.Maintenance cycle and time alarm
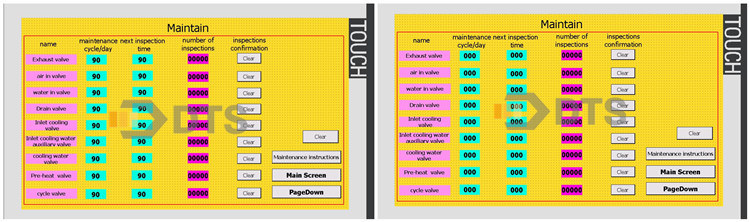
For main valves, we set the maintenance cycle and time in the PLC, when it arrives, there will be alarm appear to notice.
4. Full automatic linear control systemDTS self-studied patented technology D-TOP system can be sensitive to temperature. It can automatically calculate the pressure changes inside the container according to the temperature. And then automatically adjust the pressure inside the retort to get the pressure balance between container internal and external. So it can prevent the package's deformation, keep the package shape. Pressure was controlled in + / - 0.05 bar with compressed air intake valve and exhaust valve.
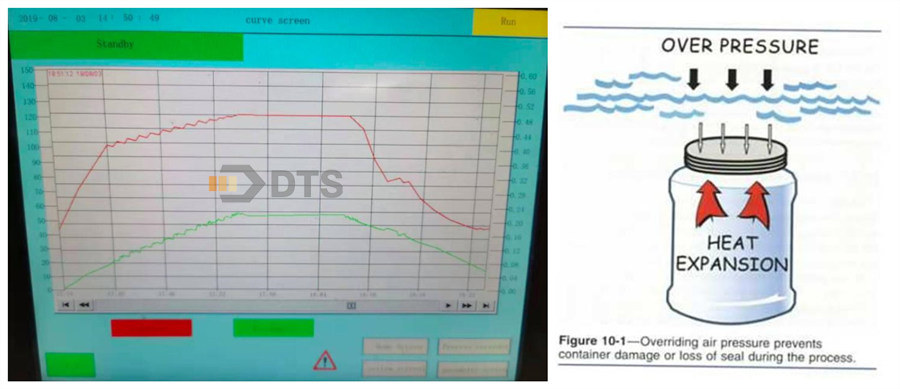
5. Double pressure control
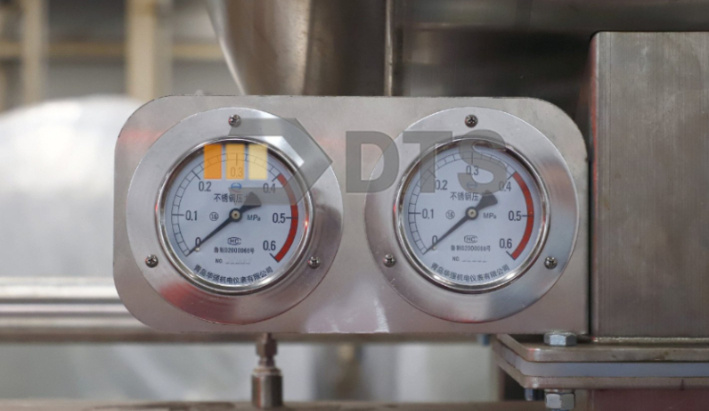
Two pressure sensors work at the same time, contrast each other, for real-time monitoring of pressure. When there is a failure, another work automatically, to ensure normal operation of equipment.
6.Heat distribution and Heat penetration (Optional)Good heat distribution result is the basis of the retort, before using the retort for sterilizing the product, heat distribution must be carried out. And as for the product process, we need to do the heat penetration to find the exact sterilization process instead of cooking too much or less. It means we can find the F0 according to the logger's data. DTS has the loggers to do these tests, we bought from America TMI, we can send engineers for this service.
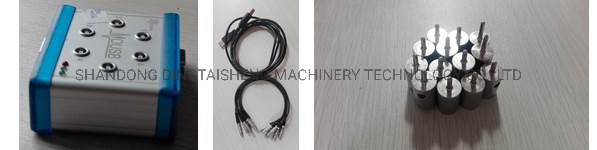
7. CNC machining centers
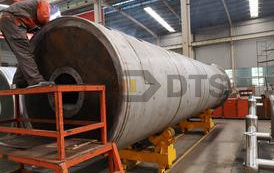
The use of special tooling and CNC machining centers, laser cutting and other equipment can ensure the accuracy of equipment processing to the greatest extent.
8. Dependable, reliable and robust designRotor is well fabricated on thepositioning& assembly station, after welding, the complete rotor isprocessed in machine center and treated in high temperature to eliminate the internal stress caused by welding, which ensures the robust structure are extremely durable resulting in reduced wear and a long service life.
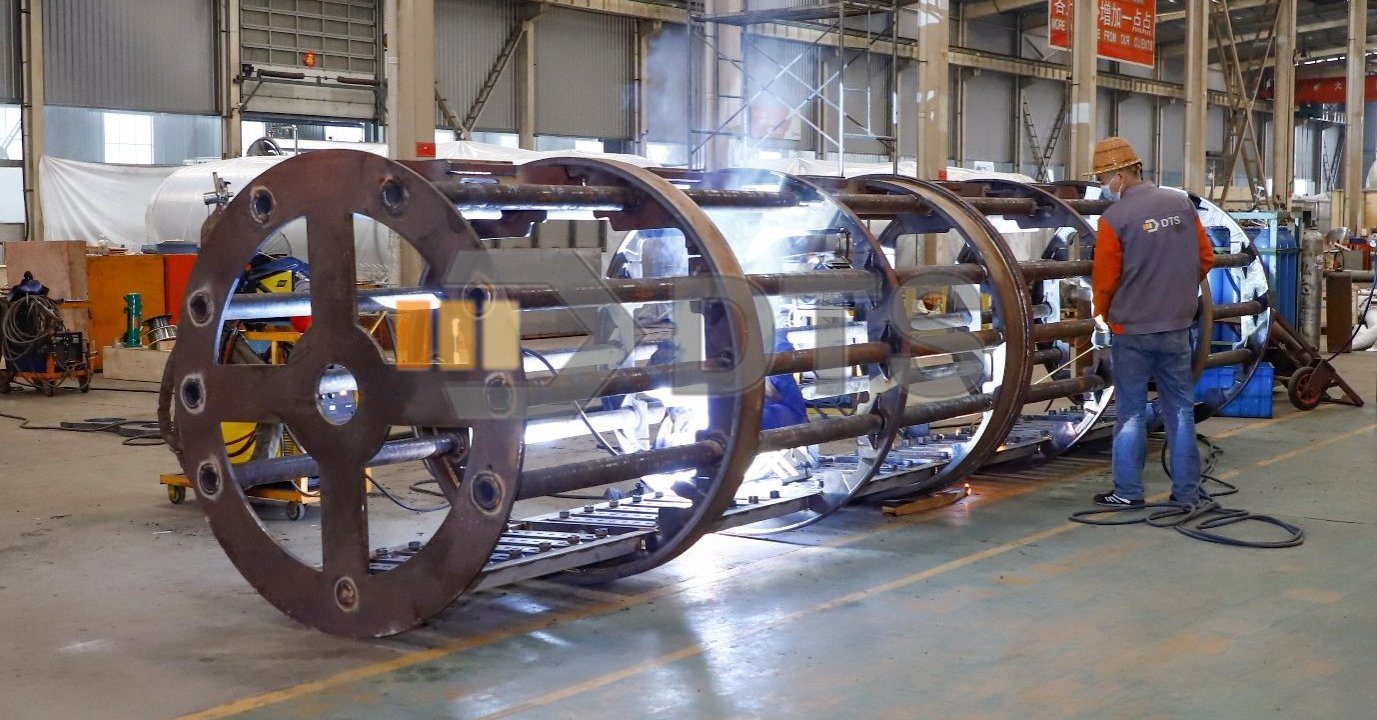
ntent="" style="background-color:#c5e1b3;padding:0 10px;margin:0;line-height:36px;">Our Advantages
1. Accurate temperature control, excellent heat distribution
The temperature control module (**** system) developed by DTS has up to 12 stages of temperature control, and the step or linearity can be selected according to different product and process recipe heating modes, so that the repeatability and stability between batches of products are maximized well, the temperature can be controlled within ±0.5ºC.
2. Perfect pressure control, suitable for a variety of packaging forms
The pressure control module (**** system) developed by DTS continuously adjusts the pressure throughout the whole process to adapt the internal pressure changes of the product packaging, so that the degree of deformation of the product packaging is minimized, regardless of the rigid container of tin cans, aluminum cans or plastic bottles, plastic boxes or flexible containers can be easily satisfied, and the pressure can be controlled within ±0.05Bar.
3. Highly clean product packaging
The heat exchanger is used for indirect heating and cooling, so that the steam and cooling water are not in contact with the process water. The impurities in the steam and cooling water will not be brought to the sterilization retort, which avoids the secondary pollution of the product and does not require water treatment chemicals (No need to add chlorine), and the service life of the heat exchanger is also greatly extended.
4. Compliant with FDA/USDA certificate
DTS has experienced thermal verification experts and is a member of IFTPS in the United States. It fully cooperates with FDA-approved third-party thermal verification agencies. The experience of many North American customers has made DTS familiar with FDA/USDA regulatory requirements and cutting-edge sterilization technology.
5. Energy saving and environmental protection
A small amount of process water is quickly circulated to quickly reach the predetermined sterilization temperature.
Low noise, create a quiet and comfortable working environment.
Unlike pure steam sterilization, there is no need to vent before heating, which greatly saves steam loss and saves about 30% of steam.
6. The rotating system has a simple structure and stable performance
The rotating body structure is processed and formed at a time, and then balanced treatment is performed to ensure the stability of the rotation
The roller system uses an external mechanism as a whole for processing. The structure is simple, easy to maintain, and greatly extend the service life.
The pressing system adopts double-way cylinders to automatically divide and compact, and the guide structure is stressed to prolong the service life of the cylinder.
ntent="" style="background-color:#c5e1b3;padding:0 10px;margin:0;line-height:36px;text-align:left;">Company Profile
ntent="" style="background-color:#c5e1b3;padding:0 10px;margin:0;line-height:36px;text-align:left;">Certifications
ntent="" style="background-color:#c5e1b3;padding:0 10px;margin:0;line-height:36px;text-align:left;">FAQ
1. How to install and maintain the machine?
The retort will be tested at the factory, and will try to ship without disassembly. All pipeline have number and identification, as shown in the picture. Also, we will provide remote service system, through which our engineers can guide and train in real time.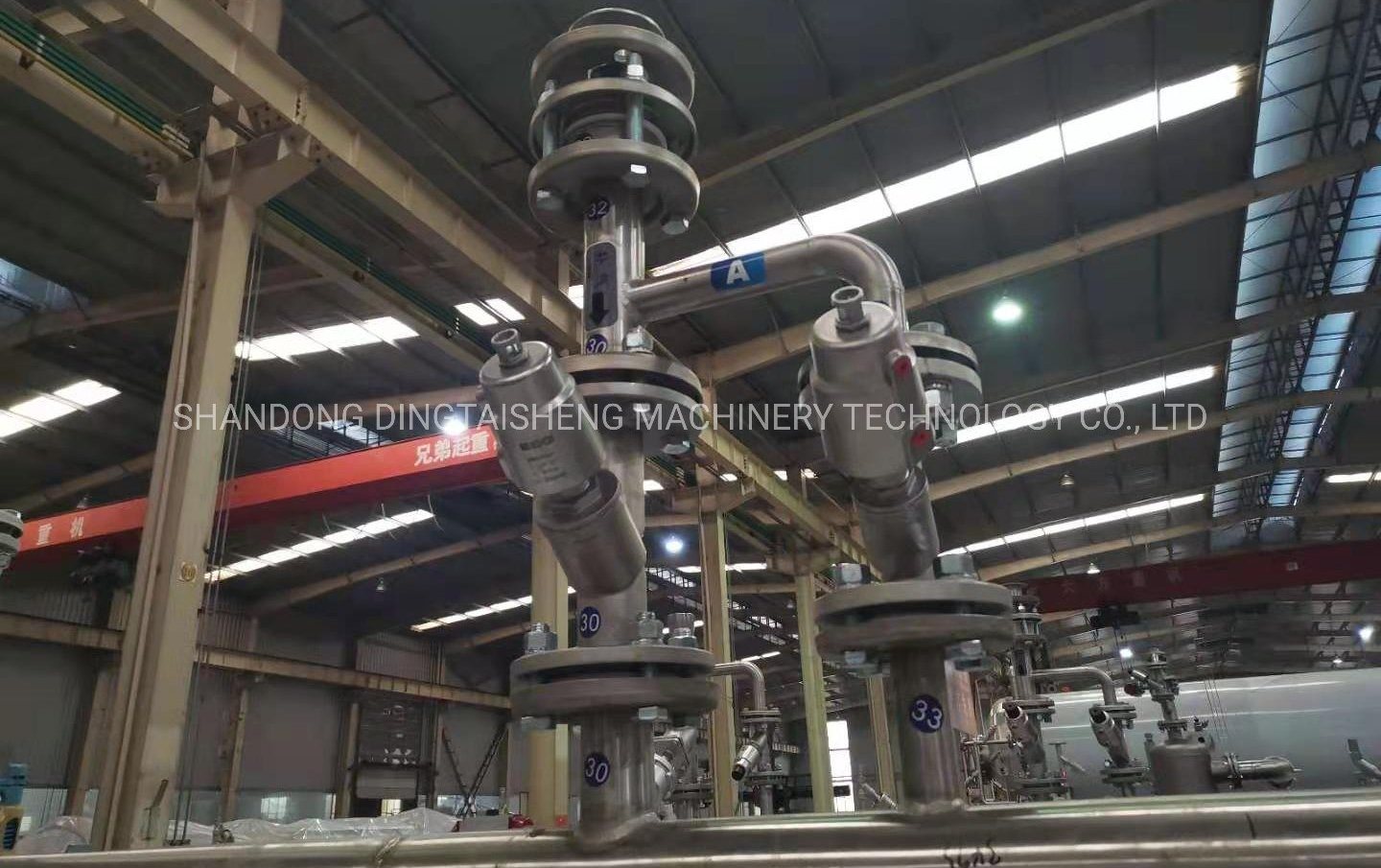
2. Are you a factory or a trader?
DTS is one of the most influential suppliers for food and beverage sterilization manufacturing industry in Asia. We have highly experienced and talent mechanical engineers, design engineers and electrical software development engineers to provide the best products and services as well as excellent working environment for our customers
3. What shall we do if breakdown occurs?
Please inform us once the breakdown occurs. During warranty period, if breakdown occurs, we shall respond in time after receiving the notification of the buyer. We shall handle failure over the telephone/real time video according to the buyer's requirements.